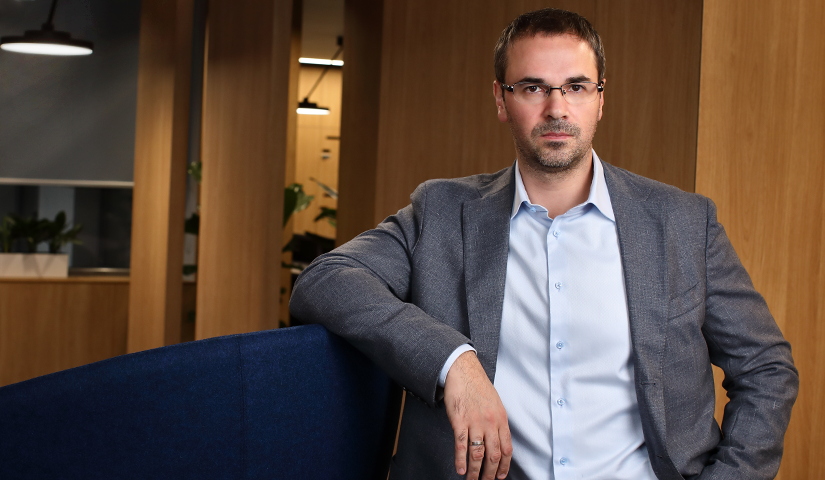
читайте также
От редакции. По просьбе HBR Россия президент НЛМК Григорий Федоришин рассказал об опыте цифровизации металлургического бизнеса и объяснил, почему компаниям не стоит бездумно гнаться за технологиями.
Группу НЛМК я возглавил в 2018 году, но мое видение цифровизации компании осталось неизменным. Я отношусь к новым технологиям прагматично — как к инструменту достижения стратегических целей. Я никогда не рассматривал цифровизацию как самоцель и пытался понять, какой именно результат мы получим. Основной стратегический фокус НЛМК — операционная эффективность, устойчивое развитие и безопасность. Если цифровизация помогает в этом — отлично, если нет, значит, она лишь красивая игрушка, которая нам не нужна.
Реализовав стратегию НЛМК на период 2013—2017 гг., мы структурно увеличили финансовый результат более чем на $1 млрд в год. Из этого эффекта почти $700 млн мы получили благодаря повышению операционной эффективности производства и вспомогательных процессов. Наши сотрудники реализовали несколько тысяч проектов и инициатив. Соответственно, мы в какой-то степени исчерпали возможности базовых инструментов бережливого производства. Чтобы наращивать эффективность высокими темпами, нужно внедрять более сложные инструменты.
В ближайшие пять лет мы планируем увеличить отдачу от проектов, связанных с операционной эффективностью, еще на $500 млн в год. И рассматриваем цифровизацию как один из доступных инструментов с хорошим потенциалом для достижения цели. Внедрить новые технологии в производственную цепочку не так сложно, гораздо труднее интегрировать их в повседневную работу сотрудников. За последние два года мы попробовали разные варианты, совершили свои ошибки и поняли, что главное — не технологии, а люди.
СТАЛЬНОЙ ГИГАНТ
Группа НЛМК — международный производитель стали с вертикально-интегрированной моделью бизнеса. Флагманский актив — Новолипецкий металлургический комбинат. Компания состоит из шести дивизионов: «Плоский прокат РФ», «Руда», «Сортовой прокат РФ», «Толстый лист Европа», «Плоский прокат Европа» и «НЛМК США», которые составляют производственную цепочку от добычи сырья до выпуска металлопродукции с высокой добавленной стоимостью. Компания является крупнейшим производителем стали в России: в 2018 году она произвела 17,5 млн тонн стали, выручка составила $12 млрд, чистая прибыль — $2,2 млрд.Первый цифровой опыт
НЛМК давно и активно использует информационные технологии, просто раньше никто не называл автоматизацию производства цифровизацией. Это как с человеком, который не догадывался, что всю жизнь говорил прозой. Автоматика и сложные системы управления стали частью металлургического производства несколько десятков лет назад. Новая волна сбора и использования данных началась относительно недавно — она вызвана внедрением инструментов бережливого производства, которые требуют применения статистических методов.
Компания генерирует огромное количество данных, только они связаны не с клиентами, как у банков или ритейла, а с различными физическими и химическими показателями процессов. Эту информацию можно обрабатывать и использовать ее для повышения эффективности производства и повышения качества конечного продукта. Поэтому два года назад в группе НЛМК появились специалисты по большим данным и математическому моделированию, мы создали центр цифровых компетенций и запустили несколько пилотных проектов.
Через некоторое время мы заметили, что часть проектов успешно завершаются, мы видим красивые отчеты, но потом эти начинания тихо «умирают». Мы стали анализировать причины и поняли, что производственные подразделения часто не понимают, зачем им нужны эти новации. А если понимают цель, то не всегда верят в реальную пользу, зато четко видят риски. Например, у мастера появился электронный советчик, который рекомендует оптимальный выбор в той или иной ситуации, например, в какой пропорции смешать сырье. Однако ответственность за результат несет мастер, а не «советчик». Цена ошибки в реальном производстве высока, как можно довериться математической модели? Еще сложнее принять такой совет, когда ты не понимаешь, по какому принципу работает «черный ящик» алгоритма, какие закономерности учитывает. В результате мастер говорит: «Отлично, спасибо!» — и продолжает работать так, как считает нужным.
То есть некоторые наши эксперименты оказались не связаны с потребностями бизнеса и жили отдельной жизнью. Мы думали в первую очередь о технических инструментах (больших данных, датчиках, искусственном интеллекте и т. п.), а не о реальных потребностях производства. Очевидно, нужно было действовать по-другому.
Мы кардинально пересмотрели прежний подход и стали создавать смешанные, или, как мы их называем, «продуктовые» команды, в которые включили производственников, технологов, специалистов по ИТ и работе с данными. При этом руководили ими именно люди с операционным опытом -– начальники производственных участков или опытные мастера.
Работа команд началась с того, что производственников попросили обозначить свои проблемы и пожелания — у кого что «болит», кому что нужно для собственных планов. В НЛМК у всех сотрудников есть цели, которые связаны с нашей стратегией. Например, мы понимаем, как через пять лет должен работать конкретный прокатный стан, каким должно быть качество выпускаемой продукции, расход сырья, время простоев и т. д., чтобы стратегия в этой части была выполнена. И каждая бригада, которая работает с конкретным агрегатом, знает, каких результатов она должна добиться. Конечно, достичь этих целевых показателей непросто, иначе все компании были бы одинаково эффективными и прибыльными. Поэтому производственный персонал с готовностью откликается, если ему предлагают помощь в решении конкретных задач.
Команды обсуждают, в каких проблемных или высокопотенциальных направлениях могут помочь цифровые инструменты, формулируют гипотезы, как это можно сделать. Сейчас у нас десять таких команд на разных площадках, они объединяют более 100 человек. Специалисты разных подразделений вместе работают над математическими моделями и прототипами и тут же на производстве их тестируют. Здесь важны вовлеченность и скорость. Когда презентуются результаты проектов, это делают сами начальники цехов — они рассказывают, как инструмент помогает им повышать операционную эффективность.
В итоге производственные подразделения приняли идею, что совместная работа направлена на решение их задач, увидели потенциал в цифровых технологиях. Мы также дали людям возможность ошибаться. Не все проекты принесли отдачу, но общий технический и финансовый эффект, безусловно, положительный.
Завод на ладони
Изначально подразделение, занимающееся в компании цифровизацией, существовало отдельно от направления классического ИТ (сюда мы включаем ИТ-системы, инфраструктуру, поддержку, безопасность). Со временем мы поняли, что это не рабочий вариант. Сейчас подразделения объединены. Такая конфигурация позволяет решить еще одну проблему цифровизации — поставить цифровые инструменты на поток, вписать их в существующие системы, обеспечить их поддержку и развитие.
В настоящее время вложения НЛМК в отдельные ИТ-системы и цифровые инструменты составляют несколько миллиардов рублей. Но как процент от общих инвестиций эти расходы относительно невелики. Все дело в том, что металлургия — капиталоемкое производство, только на поддержание оборудования в состоянии высокой производительности, на его ремонт и обновление компания тратит свыше $500 млн в год. Но требования к автоматизации и к данным всегда включаются в состав таких инвестиций, поэтому на самом деле вложения в «цифру» существенно выше.
Основное направление цифровизации на НЛМК — производство. Это наш основной ресурс для улучшений и оптимизации, основной центр затрат. Здесь выше всего отдача от внедрения новых технологий. Важно отметить, что внедрение цифровых сервисов имеет техническую отраслевую специфику. При использовании одних и тех же инструментов компании сталкиваются с разными проблемами. Например, мы работаем на многоуровневых производственных площадках, которые включают большое количество оборудования, сложные условия его эксплуатации, разные температурные режимы. Просто поставить Wi-Fi для передачи данных не получится. Нужно использовать другие технологии передачи сигнала, но это может быть дорого и небезопасно.
Еще одно существенное отличие: наше производство включает сложно моделируемые процессы. Например, еще ни у кого не получилось описать в рамках одной модели, как работает доменная печь. Сложные химические реакции протекают при высоких температурах с большим количеством расходных материалов — железосодержащего и угольного сырья, различных добавок. Такие процессы сложно моделировать, исходя из физических и химических закономерностей. Но есть и положительный момент — нейронную сеть по таким процессам можно обучать на эмпирических данных и предсказывать, как поведет себя процесс в будущем.
НЛМК постоянно занимается реконструкцией и строительством больших промышленных объектов — это проекты на сотни миллионов долларов, где важно выдерживать сроки и избегать ошибок при проектировании. Мы используем технологии компьютерного моделирования, которые позволяют создавать виртуальную копию (цифровой двойник) как самого объекта, так и процесса строительства — по времени и по стоимости. Это помогает заранее обнаружить и предотвратить ошибки в проектной документации, повысить производительность труда и снизить затраты.
Хороший пример — карьер Стойленского горно-обогатительного комбината, где мы добываем железорудное сырье и ежегодно извлекаем более 56 млн тонн руды и пустой породы. Руда залегает неравномерно, и в ней разное содержание железа. Рассчитать оптимальную разработку карьера — задача большой сложности. Наши инженеры построили цифровую трехмерную модель месторождения, визуализировали структуру запасов и условия залегания руд, а затем на основе модели разработали сценарий ведения горных работ на тридцать лет вперед. Опираясь на эти данные, мы составляем годовые и месячные планы, задания на смену и в автоматическом режиме их корректируем. Транспортные потоки в карьере также регулирует система-оптимизатор. Она направляет каждому водителю «Белаза» сообщение, где загрузить и выгрузить машину. Маршруты распределяются таким образом, чтобы руды с разным содержанием железа перемешивались, образуя однородную массу. С помощью этой системы компания увеличила объем производства железорудного сырья и оптимизировала план отработки месторождения.
Не все цифровые проекты завершаются успешно. После тестирования в течение нескольких месяцев становится понятно, что некоторые математические модели работают хуже, чем человек, они не предсказывают процесс с достаточной точностью. Причина не в том, что алгоритм плохой, просто на производстве есть процессы, где постоянно меняются входные данные. Например, мы выпускаем строительный прокат — арматуру. Сырьем для него служит лом, его состав неоднородный, контролировать его качество сложно. К тому же лом может поступать с разными добавками, причем это выясняется уже в процессе выплавки. Математическая модель основывается на данных, собранных за последние несколько лет, она советует что-то добавить или убрать во время процесса. Но она не может предугадать, что поступил новый лом, с которым компания раньше никогда не имела дело. В таких случаях правильно заниматься не компьютерным моделированием, а стабилизацией качества сырья. И здесь основной инструмент — бережливое производство, а не цифровизация.
Сейчас мы развиваем общую платформу данных и расширяем набор моделей. Планируем эти модели со временем объединять для сквозного улучшения процессов. Растет производительность труда, сложным агрегатом уже может управлять один оператор. При этом, я уверен, что, освобождая людей от рутинной и тяжелой работы, мы сможем предложить им новую и интересную деятельность в изменяющихся процессах. Тем более, что новые навыки и компетенции являются сквозными и могут применяться в разных направлениях, например, стабилизация и оптимизация процессов с помощью методов бережливого производства.
Цифровые сервисы
Помимо производства мы используем цифровые технологии и в других подразделениях компании, например, в управлении логистикой. У НЛМК сложная и высоко интегрированная производственная цепочка из нескольких заводов, в которой мы оптимизируем маршруты и запасы. «Цифра» помогает нам решать экологические вопросы, например, более эффективно очищать выбросы от вредных примесей, обеспечивать безопасность на производстве через анализ местоположения людей в реальном времени. Не стоит забывать и про внутренний клиентский сервис, когда цифровые технологии облегчают жизнь сотрудников. Сейчас мы работаем над целым набором программ, которые доступны с мобильных устройств. Помимо портала и внутренней социальной сети это, например, традиционная информация об оплате труда, расписание учебных курсов, оформление командировок и т. д.
Мы активно используем цифровые технологии для улучшения внешнего клиентского сервиса. Когда человек, например, заказывает еду или покупает вещи онлайн, он привыкает к определенному уровню сервиса — скорость, полнота информации о товаре, дополнительные опции, прозрачность статуса заказа. Хотим мы или нет, но такие же требования к сервису постепенно перетекают в B2B-сегмент. Если в банках, ритейле, телекоммуникациях и B2C-сегменте в целом эти инструменты стали уже традиционными, то в производственной сфере все только начинается. Мы создали онлайн-платформу, где у каждого клиента, оптового и мелкого розничного, есть личный кабинет, где он размещает заказы и контролирует их статус, выбирает способ доставки, ведет документооборот, общается с менеджером и т. д.
В прошлом году мы также открыли интернет-магазин для продажи стали небольшим конечным клиентам, которым, например, нужна одна машина с арматурой. Для нас это новый канал продаж и диверсификация в условиях жесткой конкуренции, для клиентов — снижение затрат и удобный сервис. Обороты быстро растут — объем онлайн-продаж в годовом исчислении уже составляет 120 тыс. тонн. Через онлайн-магазин мы можем «достучаться» до небольших покупателей, с которыми раньше не могли работать из-за слишком высоких затрат на офлайн-обслуживание. Работа онлайн помогает расширять ассортимент: мы начали включать в свою систему товары компаний, которые производят продукцию из нашей стали, а также наших партнеров — сети дистрибуции.
Используя цифровые инструменты, мы сформулировали для себя четыре урока:
1. Компания должна изначально понимать, зачем ей цифровизация, какую задачу она хочет решить и какую пользу получить. В противном случае этим лучше не заниматься.
2. Цифровые технологии нужно как можно плотнее интегрировать с бизнесом — они не должны жить своей жизнью, иначе превратятся в бесполезную игрушку.
3. Цифровизацию не следует отделять от остальной ИТ-системы — лучше строить единую структуру.
4. Основное внимание следует уделять не инструментам, а людям и новым процессам. Только тогда внедрение технологии пройдет успешно.
Об авторе. Григорий Федоришин — президент НЛМК (записала Юлия Фуколова, старший редактор HBR Россия).